Company Overview
A premier plywood manufacturing enterprise is an interior infrastructure manufacturing company, which manufactures and distributes plywood, and allied products. It has reached one of the top of the plywood industries. The company has established a strong foothold with over 30 years of experience in manufacturing and marketing a comprehensive range of plywood, block boards, decorative veneers, flush doors, and other allied products. The company has a strong leadership presence across India.
Challenges Faced
Navigating the adoption of predictive maintenance technology requires overcoming budget hurdles, employee resistance, and managing emerging risks like cybersecurity threats.
1. Adopting modern predictive maintenance tech demands significant upfront investment in sensors, data infrastructure, and analytics software. Securing budget approval and resource allocation poses challenges.
2. Resistance to change among employees is a major obstacle to implementing predictive maintenance. It arose from fear of job loss, skepticism about new technologies, or unfamiliarity.
3. Without adequate maintenance, the frequency of equipment replacements and repairs increased, leading to additional expenses and operational disruptions.
4. It brought new risks like data leaks and unauthorized access. Cyber-attacks, malware, and insider threats compromised data integrity.
Solution
Enable remote monitoring and predictive maintenance with secure IoT networks, condition-based strategies, and optimized resource allocation for efficient asset management.
1. Facilitate remote monitoring of equipment health and performance, empowering maintenance teams to oversee assets from any location and promptly address issues.
2. Secure IoT networks are crucial for effective data management in predictive maintenance. Implementing secure communication protocols, encryption standards, and access controls safeguard sensitive data transmitted over IoT networks.
3. Implement condition-based maintenance strategies, where maintenance activities are triggered based on the actual condition of the equipment rather than fixed schedules.
4. Optimize maintenance resource allocation by prioritizing maintenance activities based on equipment condition and predicted failure risks, improving operational efficiency and reducing costs.
See Gains, Check Benefits

Real-time monitoring for continuous oversight.

Early fault detection prevents downtime.
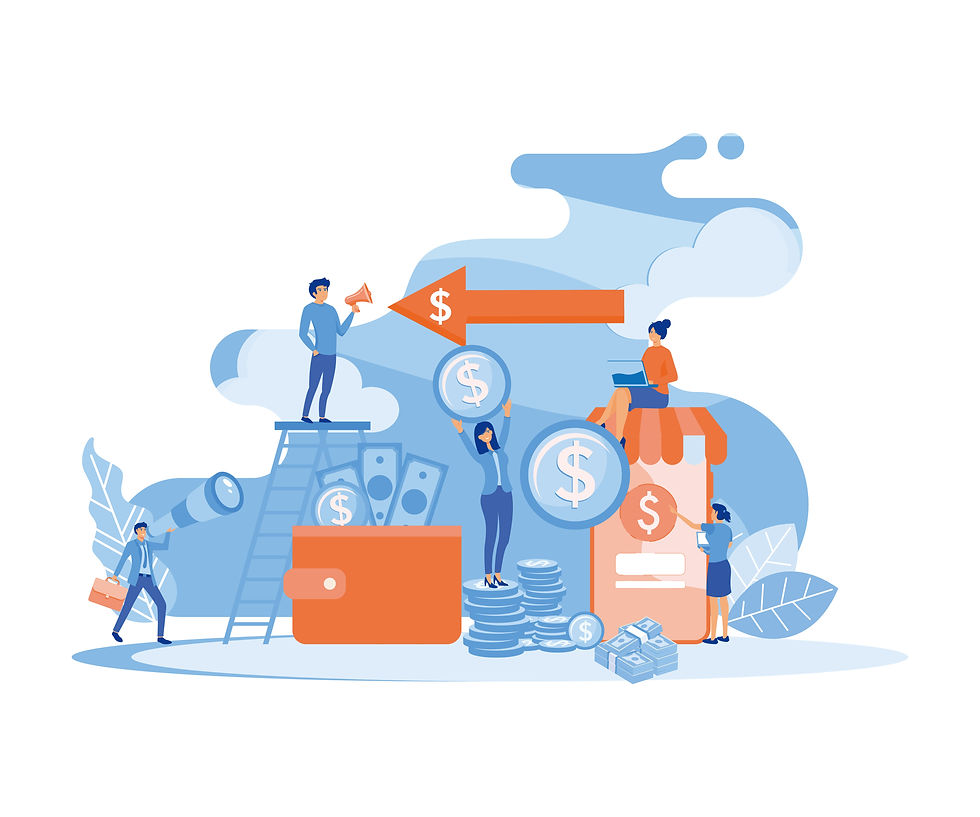
Cost savings via reduced maintenance.
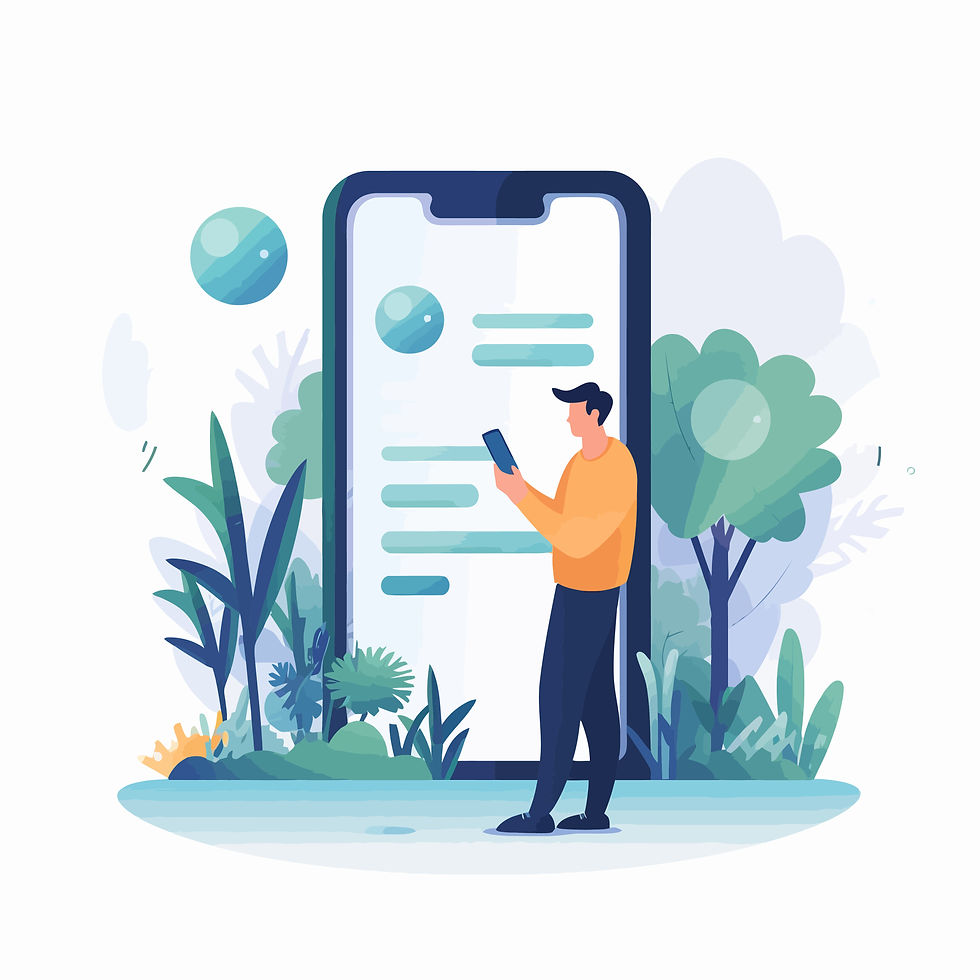
Data-driven insights optimize resource use.